Condensate management
Condensate forms anywhere where heat is released from the steam system. The saturated steam releases the heat during the transition from the gaseous to liquid phase, i.e. by condensing.
The condensate produced is at boiling point (e.g with steam pipe drainage) or is supercooled (e.g. with heat exchangers).
Although when using heat exchangers the supercooling depends on which type of heat exchanger control is used, it is frequently in the range of 10 – 30K.
In nearly all cases it makes sense, also economically, to collect the condensate produced by the heat consumers and return it to the steam boiler circuit or use it for another purpose.
Costs are reduced due to the enthalpy which is still present in the condensate, and because less freshwater is required which also means fewer surface blowdown and bottom blowdown losses.
The maximum condensate quantities of the steam consumers must be taken into consideration when sizing the condensate tank and the corresponding condensate pumps. The time delay that exists when the condensate flows to the condensate sump must also be taken into consideration. The condensate tank should always be sized so it can provisionally hold at least the amount of condensate that accumulates in roughly half an hour between the lowest and highest water level. The flow rate of the condensate pumps should be at least 3 times the hourly condensate accumulation rates during normal operation. Particular attention should also be paid to the start-up operation of the heat consumers as this is when the condensate accumulation rate is at its highest due to the heat-up operation.
Depending on the pressure and temperature level, the enthalpy of the condensate is still considerable at the normal temperatures of 80 – 140°C when compared to the make-up water which is normally cold with a temperature of around 15°C. Less freshwater and therefore fewer energy for heating up is needed as condensate is returned to the feed water vessel. In addition, condensate does not have to be chemically treated and can instead be fed directly to the feed water vessel.
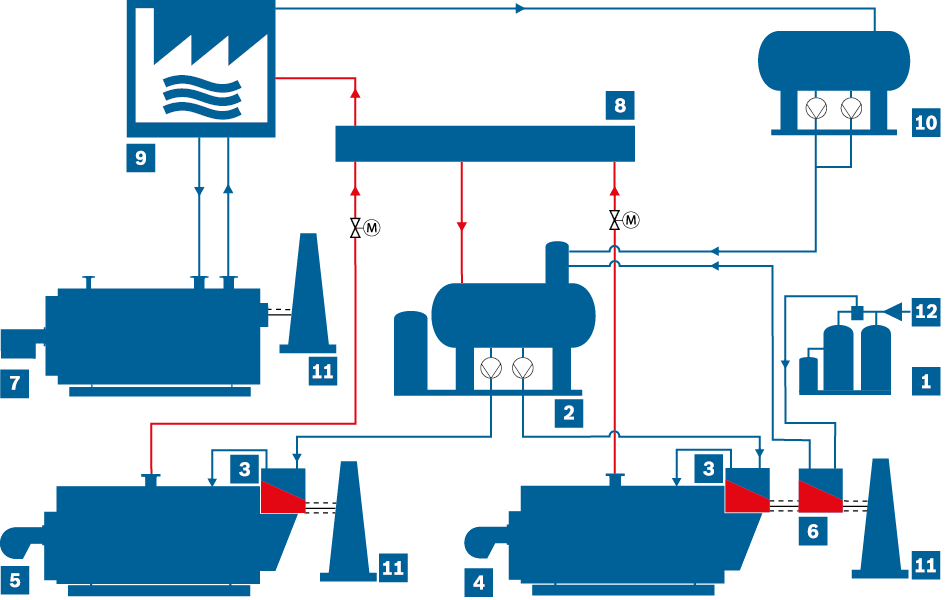
Schematic representation of an open condensate system
|
Water treatment module |
|
Steam boiler UL-S |
|
Consumer |
||
|
Water service module WSM-V |
|
Condensing heat exchanger |
|
Condensate service module CSM |
||
|
Economiser ECO |
|
Heating boiler UT-L |
|
Chimney |
||
|
Steam boiler UL-S |
|
Steam distributor |
|
Freshwater |
Expansion steam
If the condensate is collected in an unpressurised tank, this is referred to as an open condensate system. The temperature level of the condensate is then always <100°C and the condensate may absorb oxygen. In the event of a corresponding water demand which depends on the level, a condensate pump pumps the condensate back to the feed water deaeration system.
As the condensate is normally collected from several steam consumers operating at different temperature and pressure levels, the temperature of the condensate arriving in the condensate tank may also be >100°C. Expansion steam is then produced and subsequently released to the atmosphere via the exhaust vapour line and therefore represents a heat loss. These exhaust vapours can be recovered via a module, similar to the exhaust vapour module, which is installed at the feed water vessel then made available to a low temperature consumer, e.g. a heating or hot water system.
High-pressure condensate tank
If several steam consumers equipped with heating surfaces are designed for a steam pressure which remains more or less the same in the high-pressure range (> 1.5 barg), the condensate of all heat consumers can be introduced into a shared high-pressure condensate system.
Expansion steam losses therefore do not occur as a closed system is being used. As in this case oxygen does not enter the condensate during normal mode, the condensate is fed back directly into the boiler or the economiser. This means that freshwater quantities and chemical dosing are low. Outstanding savings can be achieved when using this type of system as opposed to open condensate systems with the same consumption structure.
Fuel savings of up to 12% can be achieved with a closed high-pressure condensate system. Only very little freshwater needs to be replenished and the heat energy demand for heating and deaerating is less. In addition, the surface blowdown and bottom blowdown rates are also less due to the very low salt content in the high-pressure condensate. A further benefit of closed high-pressure condensate systems is the reduced corrosion rate in the condensate network.
High-pressure condensate systems should always be used if large expansion steam losses would occur as a result of introducing condensate at a high temperature into the condensate sump or feed water vessel. Typical areas of application are breweries and paper/cardboard factories, to name but a few.
However, it is also necessary to consider that, due to the high condensate temperatures, the flue gas temperatures can increase.