Condensate management
Wherever steam is used for indirect heating in heat exchangers condensate also forms and should whenever possible be returned to the steam boiler circuit or used for some other purpose.
Reusing accumulated condensate is one of the key measures which can be taken to ensure cost-effective energy-efficient operation of a boiler system.
Condensate has two characteristics that make it particularly valuable:
- High temperatures
The condensate downstream of the heat exchanger is normally only slightly undercooled, i.e. it is at a high temperature. By recirculating the condensate, this energy content remains in the system and does not have to be expended again. - Treated water
Condensate is already treated hardness-free water with a low conductivity. Returning condensate to the steam circuit therefore saves make-up water. This means that less softening or demineralisation of water is required which reduces the amount of energy and chemicals used and these treatment systems can be sized smaller from the outset.
The condensate can be reused in different ways:
- As preheated boiler feed water
by returning it to the feed water vessel via condensate pipes and tanks or by feeding it directly into the boiler. - As hot water
for heating of processes at a low temperature level, e.g. for cleaning. - As steam
by using the expansion steam in a secondary low-pressure steam network for consumers requiring lower temperatures.
Before the condensate can be reused, it must first of all be checked for contamination and collected in a tank. This can be done either in an open or closed condensate collection system.
Info on Water quality monitoring
The differences between the two systems are highlighted in the following table:
Open system |
Closed system |
|
Container type |
Low-pressure container (0.5 – 1 bar) |
High-pressure container |
Oxygen in condensate |
Oxygenic condensate |
Oxygen-free condensate |
Condensate temperature |
≤ 100 °C |
> 100 °C |
Recirculation |
Via feed water vessel |
High-temperature feed pumps |
Condensate transportation |
Condensate pumps |
Not required |
Steam clouds |
Possible (especially with high condensate temperature of consumers) |
None |
System integration |
Straightforward |
More complex |
Investment costs |
Low |
Higher |
Energy saving |
Lower |
High |
Pipework material |
Stainless steel |
Steel |
Use of condensate |
Boiler feed water |
Boiler feed water Hot water |
Use of expansion steam |
Mainly unused In exhaust vapour heat exchanger for preheating of make-up or process water |
In the low-pressure steam network For heating of feed water vessel |
Comparison of different condensate collection systems
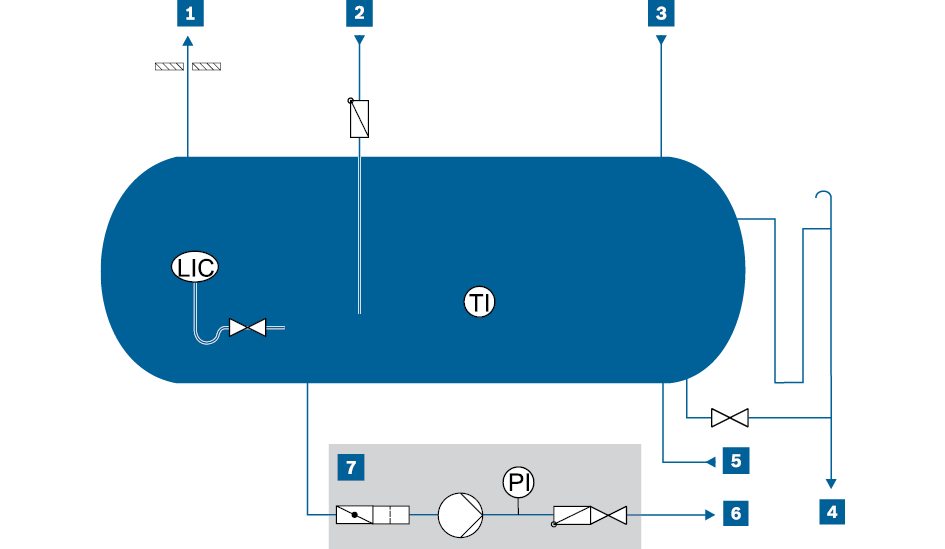
Schematic diagram of condensate tank – low pressure
LIC |
Level regulator |
TI |
Temperature indicator |
PI |
Pressure indicator |
|
Air vent line |
|
Condensate pipe leading directly to feed water module |
|
Condensate pipe, unpressurised |
|
Drain line and overflow |
|
Pump bypass pipe |
|
Line to boiler |
|
Condensate pump module |
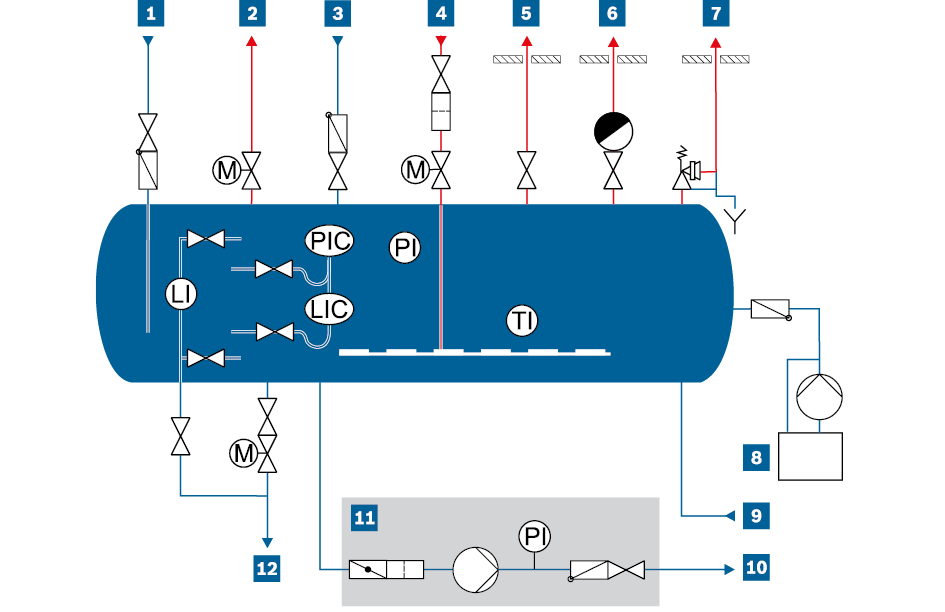
Schematic diagram of condensate tank – high-pressure
LI |
Level |
PI |
Pressure |
|
LIC |
Level |
PIC |
Pressure |
|
M |
Motor |
|
High-pressure condensate feed line |
|
Overflow steam discharge line |
|
Make-up water feed line |
|
Heat-up steam pipe |
|
Start-up line |
|
Air vent line |
|
Pressure safeguard blow-off line |
|
Chemical dosing |
|
Pump bypass pipe |
|
Line to boiler |
|
High-pressure condensate pump module |
|
Drain line |