Fewer weld seams, higher quality
Our industrial boiler manufacturing facilities are designed to handle especially wide sheet metal sections up to 3.5 metres. This means that our large boiler shells require fewer weld seams than is usually the case. A weld seam may be perfectly executed but it still cannot compete with the outstanding robustness of continuous, low-stress solid material.
Low-stress material increases the service life
Particularly tight tolerances can be achieved by using laser and plasma cutting machines to cut container and pressure vessel components. Precise angles and minimum heat input are further benefits compared to common gas cutting systems.
Cutting with CNC-controlled plasma systems ensures that less energy is introduced at the cutting points of the panels. Cutting heads which are adjustable up to 45 degrees allow simultaneous joint preparation. All boiler shells and base components are therefore processed at Bosch Industrial using this method.
Smaller sheet-metal parts for boiler components and smaller boiler shells are cut on the fully-automatic CNC-controlled laser cutting system. The workpieces which are obtained through fast, precise, low-stress cutting can be supplied to downstream processes without any reworking and with extremely small joints and burr-free edges.
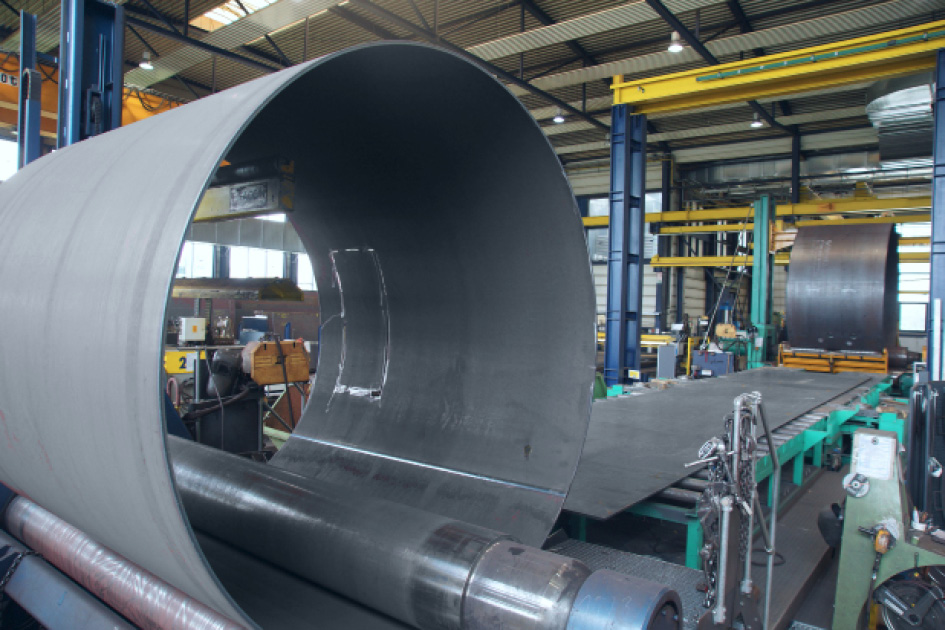