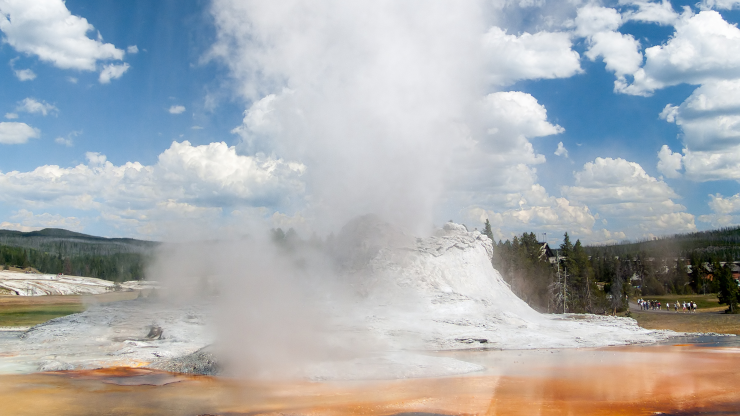
Steam
Heating of products is indispensable for many industrial processes and applications. A temperature level of between 100°C and 250°C is frequently required for this. Saturated steam or slightly superheated steam is an optimum heat transfer medium which offers many benefits:
- High energy density
- Outstanding heat transfer during condensation
- Suitable for direct and indirect heating
- Good controllability
- Water/steam is not poisonous and available everywhere
- Pumps are not required for the transportation of steam
Steam types
A differentiation is made between the following steam types:
Steam type |
Special feature |
Application |
Residual moisture content |
Wet steam |
Can cause erosion in steam pipes |
– |
> 3% |
Saturated/high-pressure steam |
The most commonly used type of steam |
Process heat < ~230°C |
theoretical: 0% |
Superheated steam |
Reduced heat losses in the steam pipes |
Steam turbines |
0% |
Low-pressure steam |
Is not subject to the Pressure Equipment Directive: More favourable installation and operating conditions are the result |
Process heat up to 0.5bar, laundrettes |
0 – 3% |
Culinary steam |
Use of non-steam volatile dosing agents |
Food industry |
0 – 1% |
Pure steam |
Generation via stainless steel pure steam generator supported by saturated steam |
Pharmaceutical industry, hospitals |
0 – 3% |
Expansion steam |
Produced by reducing pressure of pressurised boiling water |
Steam accumulator (desired) |
0 – 5% |
Differences between the individual steam types
Saturated steam or dry saturated steam
Steam which is at the border between the two steam types wet and superheated steam, is called either “dry saturated steam” or “dry steam”. It is called dry steam to distinguish its difference to wet steam. The values stated in steam tables refer to this specific state.
The physical characteristics of saturated steam are almost always used when designing heat exchangers in practise, or when calculating the steam demand of thermal processes.
However, in reality saturated steam only occurs precisely at the phase boundary. Even if it is only very slightly cooled at the same pressure it turns into wet steam or, if very slightly heated, it turns into superheated steam. If, however, the steam states are close to the phase boundary, the physical characteristics of saturated steam can be used for calculation purposes when designing a steam system.
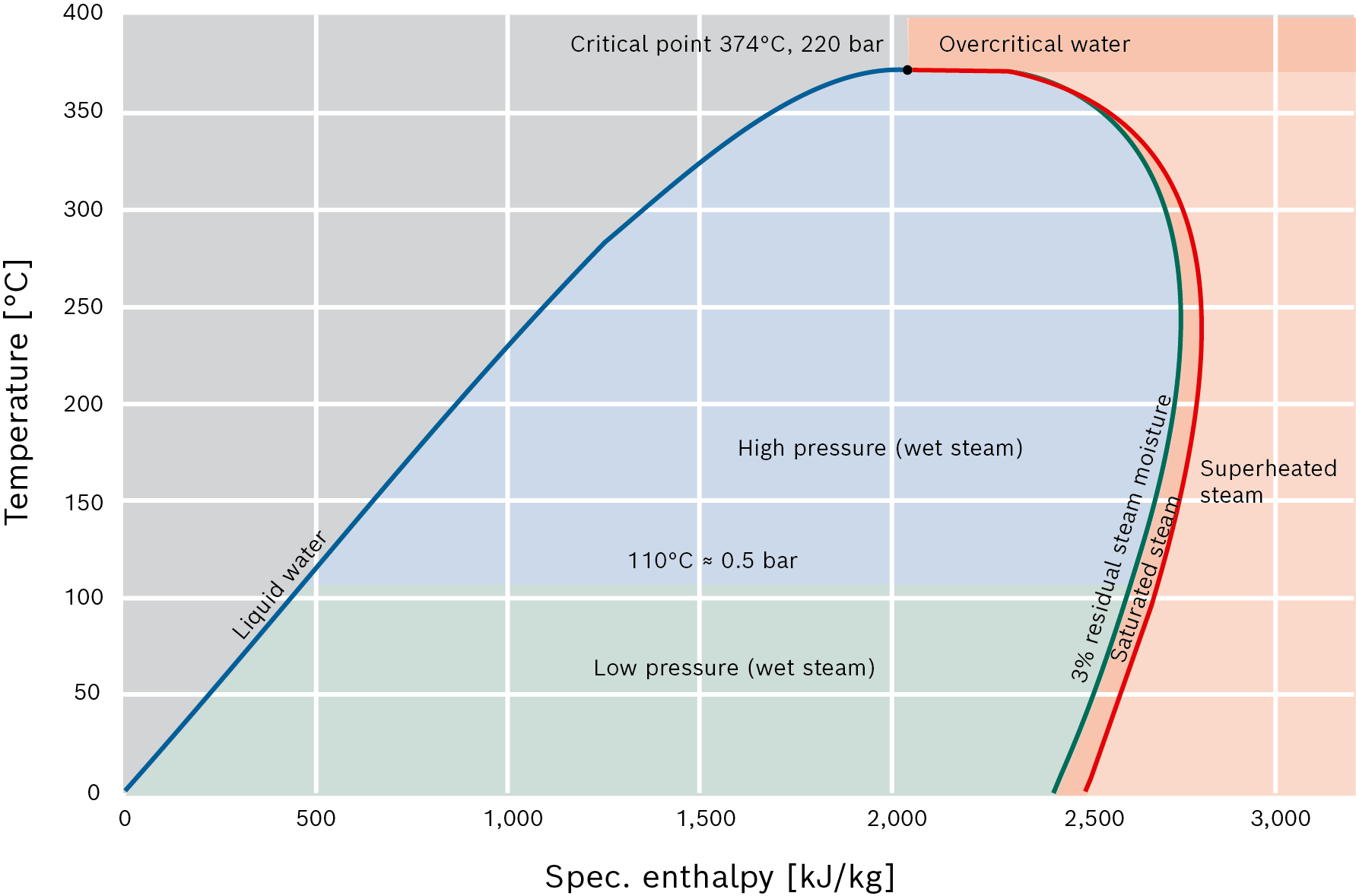
Diagram showing states of water or steam in temperature-enthalpy graph (T-h diagram) with the technical designations of the surfaces
Wet steam
Wet steam is a mixture of the liquid and gaseous phase of water. Steam with a very low mass fraction of water up to approx. 3% is also referred to in technical circles as saturated steam. This is the most common steam state which is used in industrial systems to heat products.
When steam flows out of the steam boiler, it carries along tiny droplets of water which means the steam has a residual moisture content, i.e. a liquid fraction (1 – 3% of the total mass). This residual moisture content can be reduced to roughly 0.5% of the steam quantity when exiting the boiler, by installing steam dryers for example.
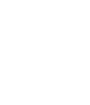
When the residual moisture content is ≤3%, this is still referred to in technical circles as saturated steam rather than wet steam. The residual moisture content is the mass fraction of water with reference to the total mass of the water/steam mixture. In addition to residual moisture content, the expression steam fraction x is also used to refer to the proportion of steam in the water/steam mixture. This is expressed in the following formula: Example at the limit of the technical saturated steam: |
Due to the heat losses to the environment that occur in all steam pipes, some of the steam condenses once again which means that in this case too damp steam with a small water fraction always exists in the pipework. This water fraction must be removed from the steam at suitable intervals by control valves and vertical sections of pipework (e.g. with condensate drains).
Wet steam with a very low steam mass fraction occurs for example during re-evaporation downstream of float-type condensate drains. In this case it is particularly important to note that the volume increases significantly during re-evaporation. This must be taken into account when sizing the condensate pipes.
Superheated steam
If saturated steam is heated further, the temperature of the steam increases with the same pressure. This is then referred to as hot steam or superheated steam. Superheated steam can be generated in shell boilers using the additional superheater module. Temperatures ≤100K above the saturated steam temperature can be achieved in this case.
Superheated steam is used to drive gas turbines or distribute steam over very large distances as condensation still does not occur despite the heat loss.
However it should be noted that the heat transfer from superheated steam until the onset of condensation is lower. This is why superheated steam is a little less suitable for heating in heat exchangers than saturated steam.
High-pressure or low-pressure steam
Steam with a pressure of p ≤0.5 bar (1.5 bara, 110°C) is referred to as low-pressure steam. Steam with a pressure of p >0.5 bar is referred to as high-pressure steam. This differentiation exists exclusively due to the regulations for installation and operation of steam boiler systems as specific operating, installation and monitoring conditions apply for high-pressure steam. As the density of low-pressure steam is very low and pipework, valves and apparatuses must be very generously sized to allow for this, it is normally only used for small steam outputs (up to roughly 3 t/h) and short distances.
Culinary steam
Culinary steam is technical saturated steam with the additional requirement that no steam-volatile dosing agents are used for alkalisation and binding of residual oxygen.
It is used, as the name implies, for the processing of food for people and animals. This steam can come into direct contact with the food (e.g. when peeling potatoes).
Pure steam
Pure steam, also referred to as ultra-pure steam, is generated in special stainless steel evaporators which are heated using normal saturated steam.
This is used in situations in particular where stringent requirements exist in relation to the sterility of the steam (e.g. in hospitals for sterilisation of surgical instruments or in the pharmaceutical industry).
Expansion steam
Expansion steam occurs at many points in a steam boiler system and therefore, must be taken into consideration.
This occurs at the blowdown expansion vessel or condensate tanks, among other places, where the expansion steam causes heat losses. Expansion steam losses can be reduced by taking appropriate heat recovery measures.
The re-evaporation of boiling water is consciously utilised in steam accumulators to provide very large quantities of steam.
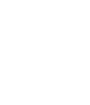
Expansion steam/re-evaporation: If the pressure of hot water in the liquid state is reduced to below the boiling pressure, some of the water evaporates and separates in the liquid and vaporous phase. During this process, the temperature of water and steam reduces to the boiling temperature of the applied pressure. This physical effect is often referred to as re-evaporation. |
Example:
Water at a temperature of T = 195°C is expanded to a pressure of p = 4 bar. The enthalpy (energy) of the system remains the same during expansion. At the same time the mass of the system also remains constant, which means that an energy balance in the form of an enthalpy balance can be established.
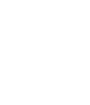
Energy in the system prior to expansion = energy in the system after expansion |
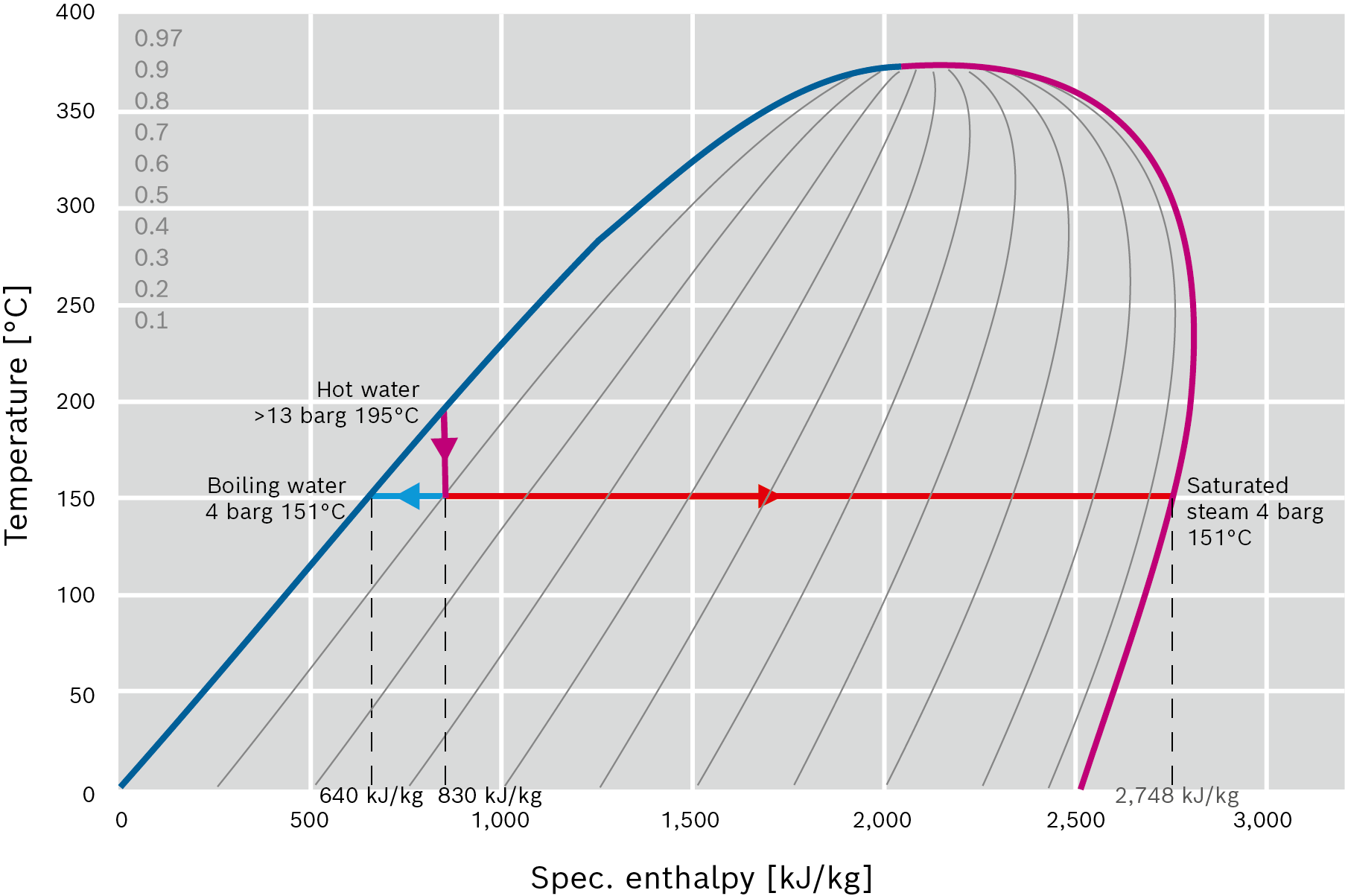