Flue gas system
The flue gas system starts where the boiler ends and has the task of removing the flue gases produced during combustion safely to the atmosphere. This includes the exhaust pipes inside and outside the boiler room, the chimney and additional built-in components such as expansion joints, silencers or flue gas dampers.
All components of a combustion system, starting with the burner with corresponding fan through to the boiler, economiser, exhaust pipes, silencers through to the chimney, must be carefully matched. Only then can problem-free operation be ensured on a long-term basis under all operating conditions. If individual components are mismatched or executed incorrectly this leads to vibrations, noises, increased emissions or unstable combustion throughout the entire system.
Flue gas systems must be sized in accordance with the national and local regulations and applicable standards.
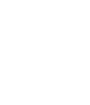
General requirements relating to flue gas systems in and on buildings are specified in EN 1443. The flue gas systems must be implemented in accordance with local building regulations. Apart from building regulations, further standards such as EN 13084-1 apply for freestanding chimneys. For definitions regarding flow sizing, see the standards EN 13384 for flue gas systems in and on buildings, and EN 13084-1 for freestanding chimneys. |
Flue gas ducts must be made of non-combustible materials and be resistant to the effects of flue gas and heat. The material of the entire steam boiler flue gas system must be suitable for temperatures up to 350°C. If the boiler is equipped with a fourth pass or a waste heat boiler for utilisation of the waste heat in flue gases from a CHP module or a gas turbine, the flue gas system must be suitable for the highest temperature that can occur in each case.
Additional country-specific requirements frequently apply for the design of the flue gas system and the height of the chimney. Only the most important functional fundamental planning principles are therefore described here.
Exhaust pipe
The exhaust pipe connects the boiler end to the inlet of the chimney. It should be routed as directly as possible, be aerodynamically efficient and have few elbows in order to keep the pressure loss and heat loss to a minimum. The pipe should not abruptly narrow or widen and instead a maximum transition angle of 30° should be used. The connection of the exhaust pipe to the chimney should always be established by tapping into it at an angle of 30 – 45°.
Requirement |
Design |
Constant combustion chamber conditions |
Designed for +0/-1mbar at boiler end One chimney draught recommended per boiler |
Low pressure loss |
Short, few elbows and aerodynamically efficient |
Low heat loss |
Provide insulation |
Remove condensate |
Condensate drainage nozzle and neutralisation |
Ensure unrestricted passage |
Provide cleaning and inspection apertures |
Emission measurement |
Provide emission measurement nozzle |
Cleaning and inspection |
Provide cleaning and inspection apertures at all deflections |
Compensate for thermal expansion |
Provide expansion joints |
Resistance |
Temperature resistant (up to 350°C), condensate resistant, corrosion resistant |
Compression strength |
Positive and negative pressure |
Gas tightness |
Gas tightness according to EN 1856 |
Danger due to insufficient air |
Integrate flue gas and supply air flaps with safety-orientated limit switches |
General requirements for exhaust pipes
Sizing
The exhaust pipe with all components such as flue gas dampers, expansion joints and silencers can normally be continued up to the chimney with the same nominal diameter as the flue gas connector at the boiler.
When designing the system, a recommended speed of 16.5m/s with reference to the boiler outlet temperature should not be exceeded. As the recommended speed is referenced to the operating flow rate, the flue gas mass flow rate which is normally specified still has to be converted to the operating flow rate.
The ideal gas law can be used for the conversion.
Example, natural gas H:
λ = 1.15 Excess air
ṁ̇FG = 10,000 Flue gas mass flow rate [kg/h]
pn,FG = 1.244 Standard density of flue gas [kg/m³n]
Tb = 250 / 523.15 Flue gas temperature [°C]/[K], downstream of boiler and upstream of economiser
pb= pn = 1.01325 Ambient pressure [bar] (deviation from the standard condition is disregarded)
The draught calculation of the chimney manufacturer may also require a larger nominal diameter, especially where short chimneys and long exhaust pipes are concerned.
Flue gas silencer
The purpose of flue gas silencers is to reduce the emission of combustion noise. To guarantee effectiveness of the silencer, it must be designed for the frequencies emitted by the burner, the boiler output and the specified approved noise emissions.
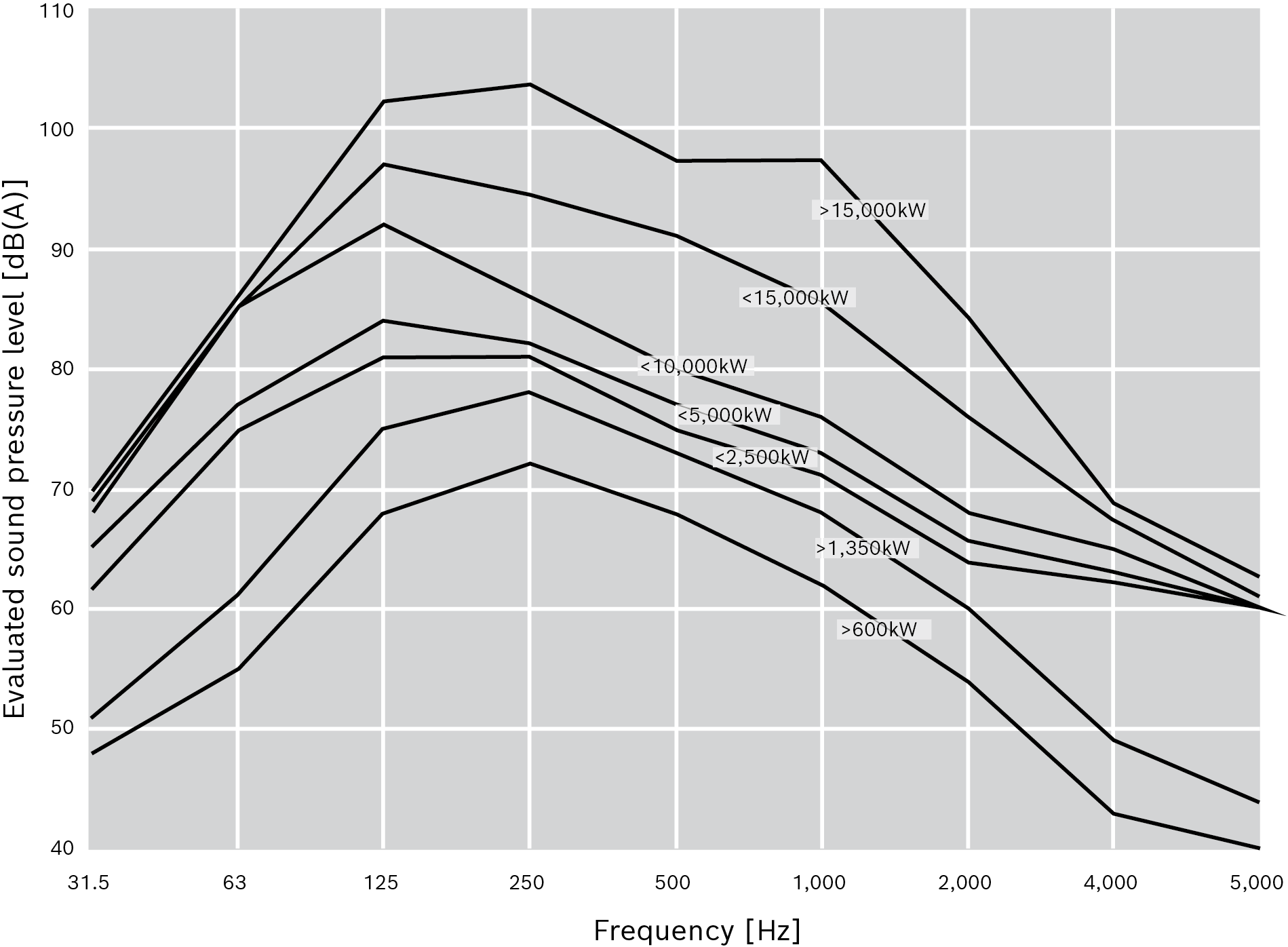
A-rated frequency analysis and corresponding total sound pressure level with reference to boiler output
Boiler output |
[kW] |
≤ 600 |
≤ 1,350 |
≤ 2,500 |
≤ 5,000 |
≤ 10,000 |
≤ 15,000 |
> 15,000 |
Empirical value for the total sound pressure level |
[dB(A)] |
75 |
81 |
85 |
87 |
94 |
100 |
107 |
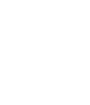
The values shown in the figure above (A-rated frequency analysis and corresponding total sound pressure level with reference to boiler output) are only guide values for a single boiler without flue gas silencer. The measurement was performed 1m from the chimney outlet at an angle of 45°. |
The noise produced during combustion is emitted as airborne noise via the surface of the flue gas system and emerges at the chimney head. The noise from a boiler system primarily consists of low frequency sound.
These sound emissions can be effectively reduced with a flue gas silencer. To comply with the prescribed sound emission values when designing a flue gas silencer the frequency spectrum of the flue gas noise at the chimney outlet of the boiler system must be taken into consideration.
The graph in figure (A-rated frequency analysis and corresponding total sound pressure level with reference to boiler output)
shows the average sound pressure level of a boiler, measured at the chimney outlet with no flue gas silencer in the flue gas system. As the combustion system (e.g. due to the burner construction or the flow profile that occurs in the combustion chamber) and flue gas system (e.g. due to the number of elbows, length and diameter of the exhaust pipe) have a considerable influence on the resulting values, only guide values can be specified here for the sound pressure level. In the case of the multi-boiler system the sound levels of all boilers must be added up.
When planning the exhaust pipe, it must be considered that to reduce the noise emissions, the silencer must be fairly long, depending on the requirement, and must be installed inside or outside the installation location prior to entry of the exhaust pipe into the chimney.
If the sound emission requirements are exacting, e.g. in the hospital sector, due to the complexity of the topic, it is advisable to consult an acoustics expert regarding the specific design of the flue gas silencer.
Chimney
The purpose of the chimney is to remove the flue gas and pollutants it contains harmlessly to the surroundings by ensuring they are removed in the free air current without disruption and are also sufficiently diluted. It should be in the immediate vicinity of the boiler house to avoid long flue gas ducts and the flue gases should be removed vertically upwards. Obstruction of the free air flow by elbows or rain canopies is not permitted.
Chimney height
The minimum required height for the chimney is defined by the national requirements for air pollution control.
Chimney cross-section and chimney draught
The temperature of the flue gases in the chimney is higher than the outdoor air. This produces a lifting force, the so-called “chimney draught”, in the chimney and rising exhaust pipe sections. This supports the removal of the flue gases and produces a negative pressure in the chimney and sections of the exhaust pipe. The size of the chimney draught is also linked to the temperature difference in relation to the atmosphere via the density.
The chosen chimney cross-section must be large enough to allow the lifting forces to overcome the flow resistance in the chimney from the boiler end. On the other hand, the cross-section should not be too large to ensure the flue gases still exit the chimney at a velocity of at least 6m/s and so that an overly high negative pressure does not exist at the boiler end, especially with very high chimneys.
The calculation for the exhaust pipe should always be performed by a specialist contractor or the boiler manufacturer.