Types
Due to the following requirements for steam boilers, various types have emerged:
- Installation
- Operation
- Steam pressure and steam output
- Low-emission combustion systems
- High efficiencies
3-pass boiler
The 3-pass boiler consists of three horizontal flues built into a large cylindrical pressure vessel closed at each end by two level bases. All flues are located in the water space, which takes up roughly 75% of the area. The steam space is located above this. These boilers are also referred to as shell boilers and contain a large volume of water.
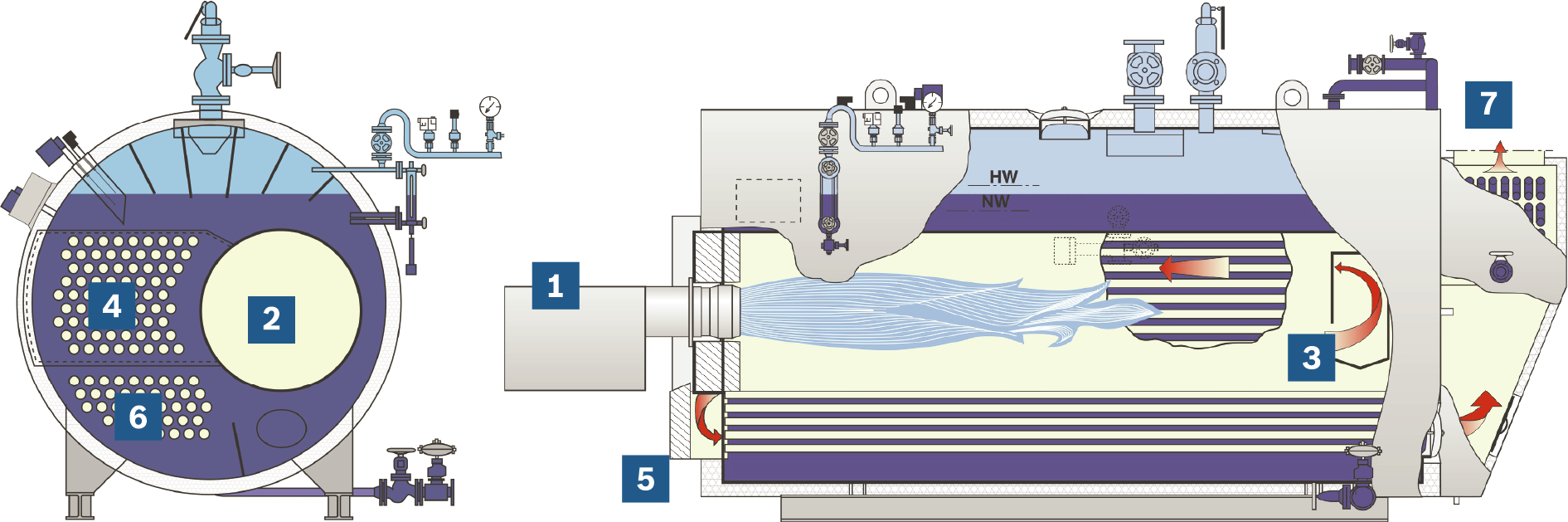
3-pass shell boiler
|
Burner |
|
Smoke tube pass (pass 2) |
|
Flue gas connection for economiser |
||
|
Flame tube (pass 1) |
|
Front reversing chamber |
||||
|
Internal reversing chamber |
|
Smoke tube pass (pass 3) |
Combustion takes place in pass 1, the flame tube. Roughly half the heat is transferred here, primarily by means of thermal radiation to the flame tube walls. The combustion is complete at the end of the flame tube and the flue gases are diverted in the internal water-cooled reversing chamber into pass 2.
Roughly 35% of the thermal output is then transferred in the pipe panel of pass 2. The flue gases then enter the reversing chamber at the front on the outside at a temperature of ~400°C where they are redirected to pass 3.
After pass 3, the temperature of the gases is still normally 200 – 280°C, depending on the temperature of the medium in the water chamber of the boiler.
This heat potential can then be further utilised in an integrated economiser so that a temperature of 90 – 140°C is reached at the flue outlet.
This allows single flame-tube boilers to reach a steam output of up to 28,000kg/h.
Double flame-tube boilers can be used to achieve higher outputs. These boilers feature two flame tubes with separate second and third smoke-tube pass arranged in parallel in the water space. This allows boilers with steam outputs of up to 55,000kg/h to be built. The unrestricted single flame-tube operation also increases the reliability and control range of the boiler.
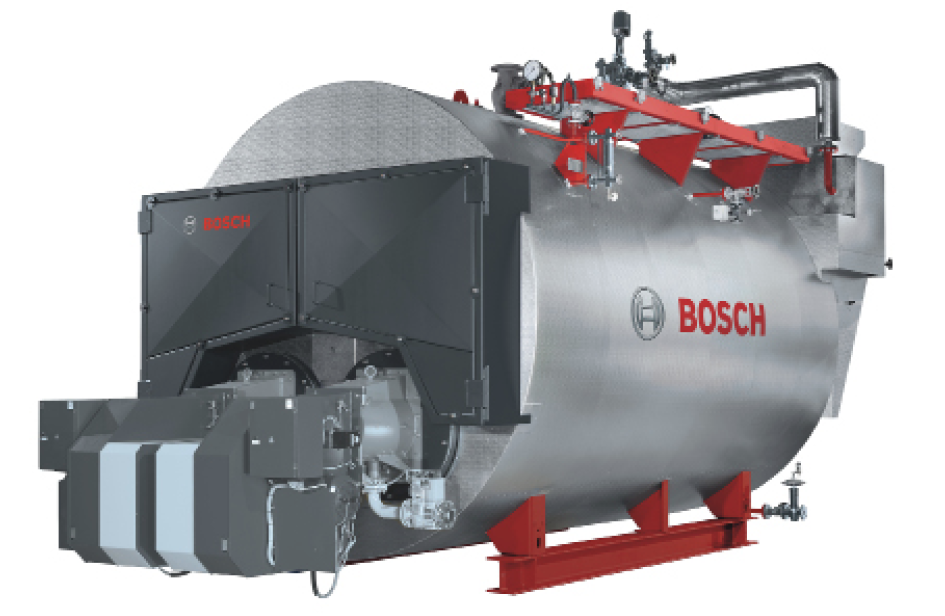
Reverse flame boiler
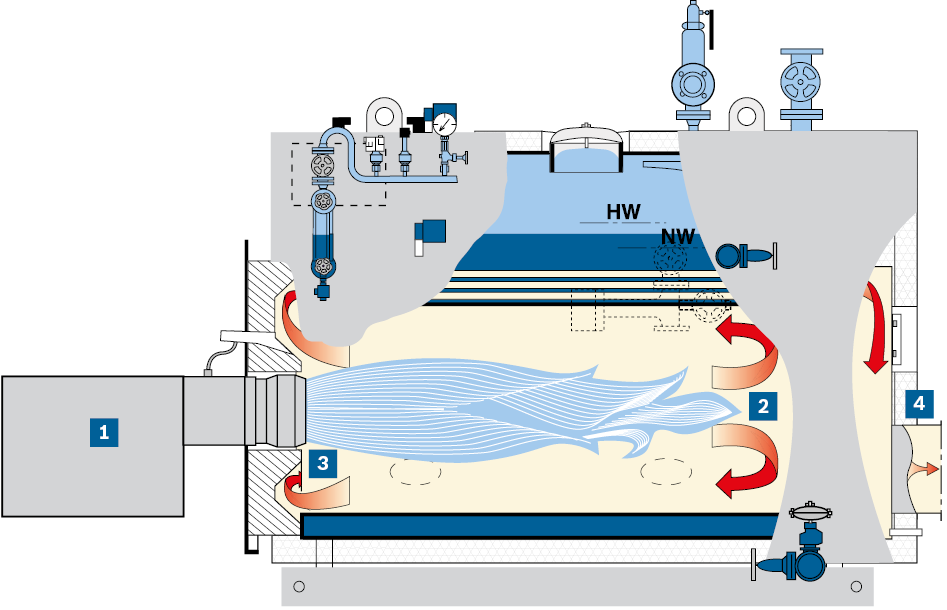
Reverse flame boiler
|
Burner |
|
Internal reversing chamber |
|
Front reversing chamber |
|
Flue gas connection for economiser |
The reverse flame boiler was developed as steam boiler for small outputs of 175 – 3,200kg/h. In this boiler, the flame tube is arranged centrically and the flow direction is reversed at the end of the flame tube so that the flue gases inside the flame tube flow back towards the front. This is why it is called the reverse flame boiler. In the front reversing chamber, the flue gases are then diverted into the tube array around the flame tube. This type is characterised by a very compact design. Oil or gas can be used as the fuel.
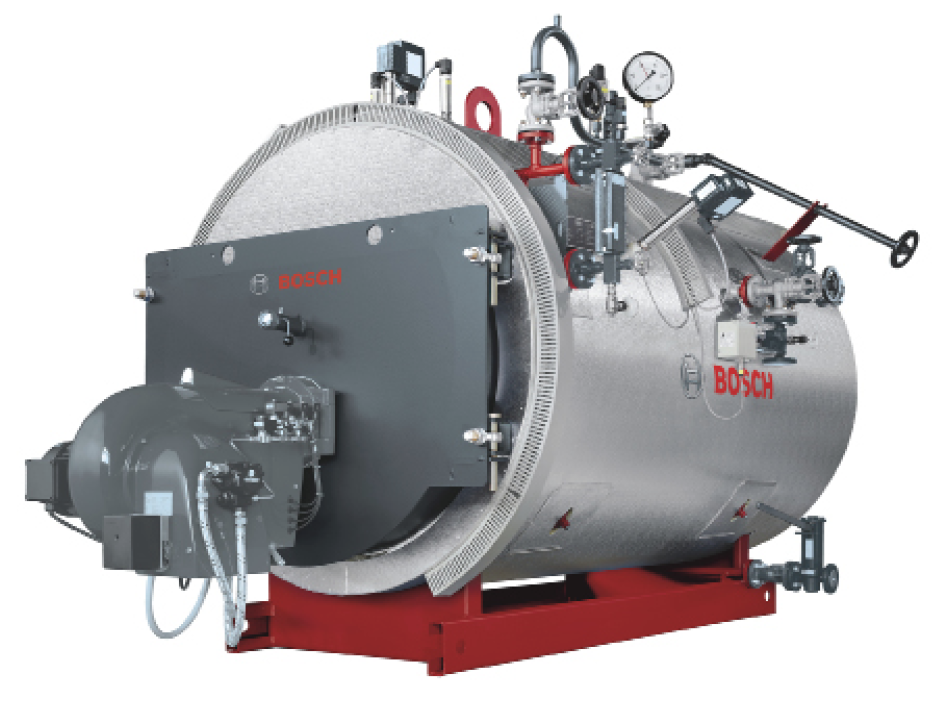
Boiler with waste heat utilisation
A 4-pass boiler or pure heat recovery boiler is a special type of boiler which utilises waste heat to generate steam. With the 4-pass boiler, part of the third smoke-tube pass is used as a separate pass for through-routing of hot flue gases and delivers up to 15% of the energy supplied. A pure heat recovery boiler has no burner. It obtains all of its energy from hot flue gases (e.g. from CHP modules or gas turbines).
Quick steam generator
Due to its design, the quick steam generator belongs to the family of water tube boilers whose pressure system consists of one or several coils. Water flows through the coil(s) and is heated from the outside by the flue gases. Quick steam generators operate according to the once-through forced-flow principle which means the water evaporates completely in one cycle. Only a small amount of energy is stored in the water chamber. These boilers can therefore reach their full output within a few minutes after starting from cold, which is also why they are referred to as quick steam generators. They are heated by oil or gas-fired pressure-jet burners and the output regulation must always be adjusted to the quantity of water running through.
Shell boilers |
Quick steam generator |
|
Water content |
Large water content |
Small water content |
Heat-up duration |
Longer |
Cold start within several minutes |
Response to load fluctuations |
Damping of load fluctuations of consumers High short-term overload possible when using steam accumulators |
High-pressure fluctuations even with slight load variations at consumers |
Steam moisture |
Dry steam |
Steam dryer required |
Approval of installation and monitoring1) |
Normally subject to mandatory approval and monitoring |
The installation and monitoring conditions have been partially eased in the very small output range |
Procurement costs |
Slightly higher |
Lower |
Operating personnel1) |
Qualified boiler attendant required1) |
Trained operating personnel required1) |
Maximum steam output |
≤ 55,000 kg/h per boiler |
≤ 2,000 kg/h per boiler |
Efficiency |
94 – 105 % therefore ideal for continuous operation |
< 90 % therefore only suitable for short-term provision of steam at short notice |
Annual degree |
≤ 95 % |
Frequent < 75 % |
Service costs |
Lower |
Higher |
Service life |
Robust, low wear, therefore durable |
Low |
1) Refers to Germany