Welding with precision
Thanks to our process cranes with exceptionally high load-bearing capacity and our high production halls, boilers weighing up to 120 tons can be safely, quickly and gently turned and set up in the ideal processing position. By contrast, in older production facilities boilers weighing more than 60 tons, for example, are often welded out of necessity in a sloping position. This can lead to quality problems with the weld seems.
Horizontal welding allows a more homogenous structure to be achieved, a higher penetration depth, notch-free geometries, outstanding welding quality and therefore greater uniformity of the welding process in general.
For the individual assembly of a boiler with flanges and customised equipment, the components are connected manually using the metal active gas welding (MAG) procedure.
To ensure pore-free seams it is essential that the inert gas is not blown away during welding. We ensure this by protecting our work areas with windprotected work stations, special ventilation systems and radiant ceiling heating instead of conventional hot air blowers.
Our globally unique, self-developed corrugated tube machine is able to manufacture fully automatically corrugated flame tubes with up to 9 metres length. The machine is equipped with twelve servomotors and three lasers for monitoring and control. It manufactures corrugated flame tubes with millimetre precision using laser technology. Corrugated flame tubes are a core product in boiler manufacturing and are the components that must withstand the highest stress.
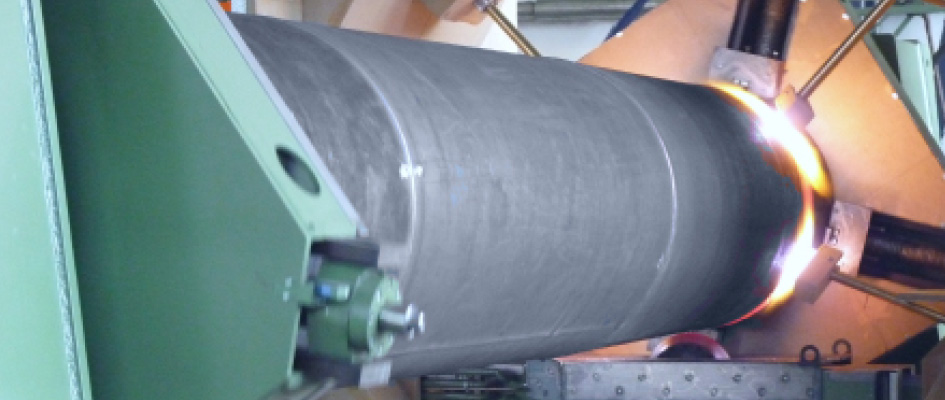