Aumento de la eficiencia del sistema de quemadores
Ventilador de aire de combustión
Se requiere una mezcla óptima de combustible y aire para lograr una combustión completa. Sin embargo, las calderas industriales suelen funcionar a carga parcial. En este modo de funcionamiento se reducen tanto el suministro de combustible como el de aire.
El ventilador de aire de combustión sin regulación de velocidad también funciona en los rangos de carga parcial a velocidad nominal, ya que en este caso la cantidad de aire suministrada para la combustión se limita únicamente mediante el cierre de las compuertas de aire. En este caso el ventilador consume una gran cantidad de energía eléctrica que desaparece sin ningún beneficio debido a la restricción. Si la cantidad de aire se modifica principalmente mediante la modulación de la velocidad del ventilador, el consumo eléctrico en los rangos de carga parcial es mucho menor.
El comportamiento de generación de ruido también va en la misma línea que la reducción del consumo eléctrico. Todos los sistemas que suelen funcionar en rangos de carga parcial durante periodos prolongados deberían estar equipados con ventiladores de velocidad regulada.
Se puede ahorrar alrededor del 40 % de la energía eléctrica utilizando un perfil de carga del quemador con una utilización media de la capacidad. Con ello se consigue normalmente un ahorro anual de cuatro cifras en euros, lo que significa que un quemador con control de velocidad se amortiza normalmente en un año.
Ejemplo: |
|
Potencia de la caldera |
10 t/h |
Ventilador del quemador |
22 kW |
Ahorro de electricidad |
cerca de 48,000 kWh/a (42 %) |
Ahorro de costes |
cerca de 6,720 €/a (precio de electricidad 0.14 €/kWh) |
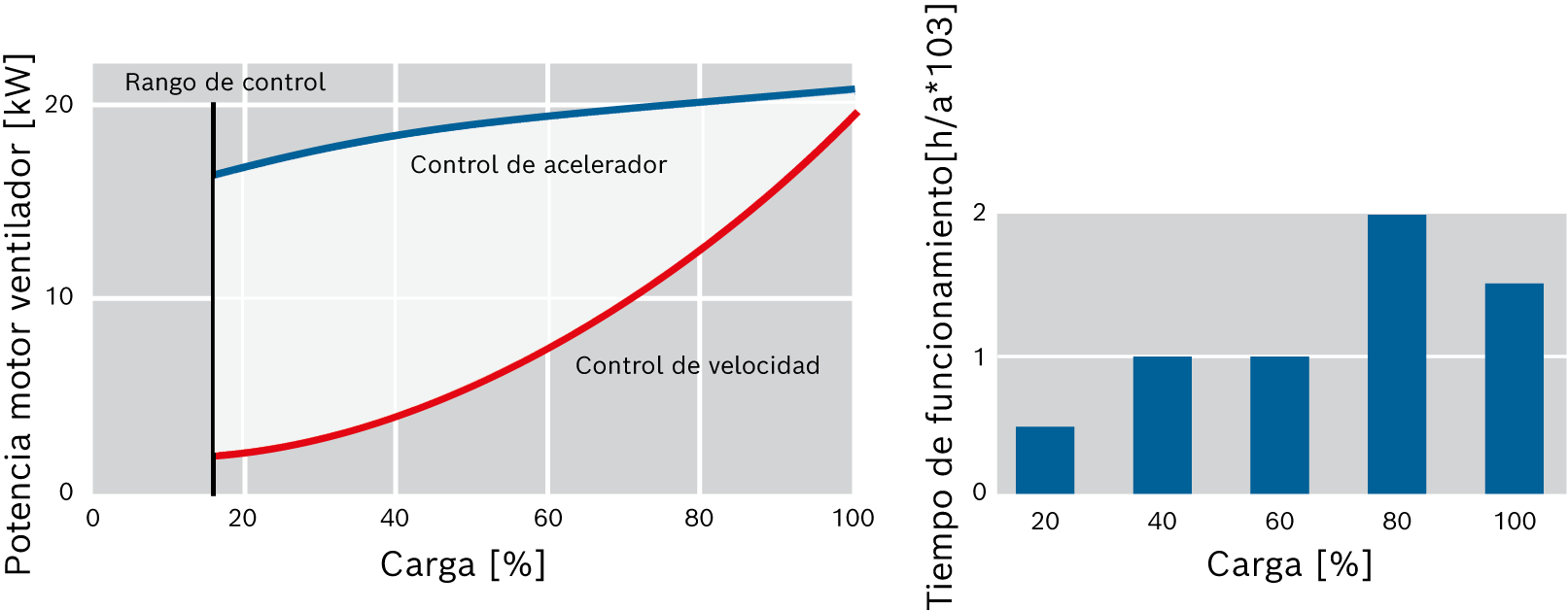
Ahorro de energía con el ventilador del quemador de velocidad controlada
Exceso de aire
En la tecnología de la combustión, la situación ideal es la combustión estequiométrica. Esto ocurre si todas las moléculas de combustible reaccionan completamente con el oxígeno sin dejar combustible u oxígeno sin quemar.
Si no se suministra suficiente oxígeno atmosférico durante el proceso de combustión, puede producirse una reacción de combustión incompleta. Una consecuencia negativa de ello sería la formación de monóxido de carbono, un gas altamente tóxico. Si la cantidad de aire aumenta demasiado rápido, todas las moléculas de combustible ya han reaccionado con las moléculas de oxígeno. Las moléculas de oxígeno restantes forman un excedente que no se necesita. Como normalmente se utiliza el aire frío del ambiente como aire de combustión, este aire frío se acaba calentando con un volumen innecesariamente alto de aire sobrante, que se libera a la atmósfera junto con los gases de combustión.
Por lo tanto, un ajuste óptimo del aire de combustión es importante para un funcionamiento eficaz y una combustión segura y limpia. Esto es atribuible, por un lado, a las fluctuaciones de la presión, la temperatura y la humedad del aire y, por otro, a las fluctuaciones de la calidad del combustible, que aumentarán. Por otro lado, debe especificarse una cierta cantidad de exceso de aire en comparación con el ideal teórico para proporcionar un margen de seguridad. Por último, no debe permitirse en ningún caso la formación de monóxido de carbono, un gas venenoso y explosivo. Estos ajustes se realizan y comprueban normalmente al poner en servicio el sistema de calderas y al realizar el mantenimiento trimestral o semestral.
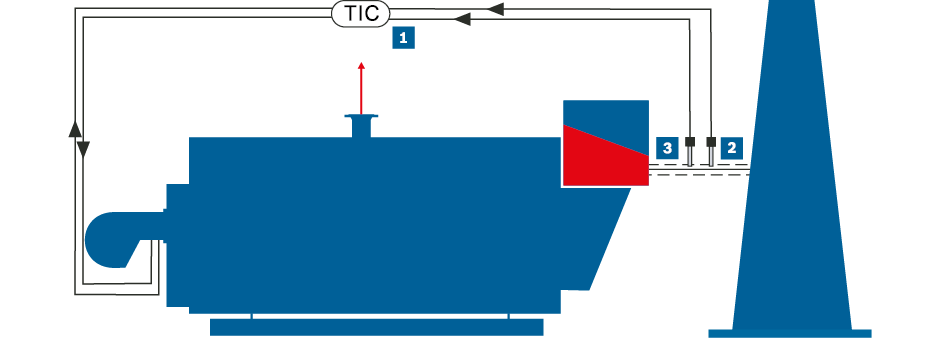
Control O2 y CO en la caldera de vapor (representación simplificada)
|
Control |
|
Sonda de prueba de O2 |
|
Sonda de prueba de CO |
|
Vapor |
|
Gases de combustión |
Además, para poder operar los sistemas más cerca del punto de funcionamiento óptimo en condiciones variables, se necesitan unidades de medición y control continuas. Un control de O2 consiste esencialmente en una sonda de medición de oxígeno que se instala en el flujo de gases de combustión y una unidad de control. Esta registra continuamente el contenido residual de oxígeno en los gases de combustión y envía la señal al control del quemador, que ajusta la cantidad de aire según sea necesario.
Desde hace algunos años se dispone de electrodos combinados (O2 y CO). En combinación con la medición de CO, el exceso de aire λ puede ajustarse con mayor precisión al límite de CO. Cuando se utiliza un control de O2 y CO, el ajuste utilizado normalmente para el exceso de aire a plena carga de 3 – 4% en vol. de oxígeno en los gases de combustión puede reducirse a 0.5 – 1.0% en vol. de oxígeno. Esto equivale a una reducción de la pérdida de gases de combustión de aproximadamente 1 punto porcentual a la misma temperatura de los gases de combustión. El control de O2 y CO no puede utilizarse cuando se utiliza aceite como combustible.
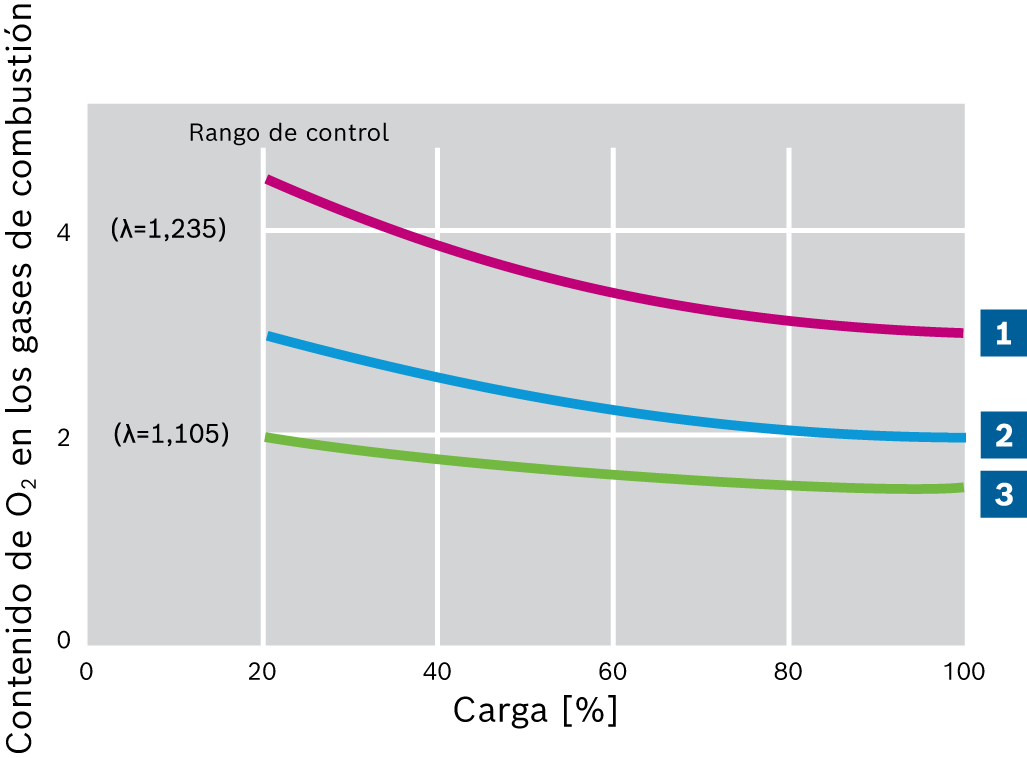
Contenido residual de oxígeno y exceso de aire mediante el control de O2 y CO a través de la carga del quemador
|
Sin control |
|
Sin O2 control |
|
Sin CO control |
Ajuste de la potencia
En las instalaciones existentes, y también ocasionalmente en las nuevas, la potencia disponible de la caldera es muy superior a la potencia real de vapor necesaria.
Las causas de ello son frecuentes:
- Reducción de la demanda en sistemas existentes, por ejemplo, porque ya no existen consumidores o porque se han aprovechado posteriormente los potenciales de recuperación de calor existentes.
- Sobredimensionamiento durante la planificación de nuevos sistemas, por ejemplo, debido a factores de diversidad incorrectos de los consumidores, a la consideración de reservas de energía demasiado elevadas o a una ampliación de los consumidores que ya se ha tenido en cuenta pero que aún no se ha llevado a cabo.
Como consecuencia, la tasa de extracción de vapor es demasiado baja en relación con la potencia de la caldera, lo que provoca un elevado número de operaciones de encendido y apagado del quemador. Esto provoca pérdidas de preventilación y también tensiones debidas a fluctuaciones de temperatura que pueden ser extremas, especialmente con tiempos de preventilación largos.
Se pueden tomar las siguientes medidas para compensar una potencia de caldera demasiado elevada:
- Instalación de controles de baja carga que pospongan la subida inmediata tras el arranque del quemador
- Utilización de reguladores de potencia que permiten que el quemador se adhiera a la etapa de carga baja durante un periodo ilimitado
- Utilización de quemadores con un rango de control elevado
- Adaptación de la potencia del quemador a las necesidades reales. Para ello es necesario modificar el quemador o añadir un quemador con un rango de potencia menor.
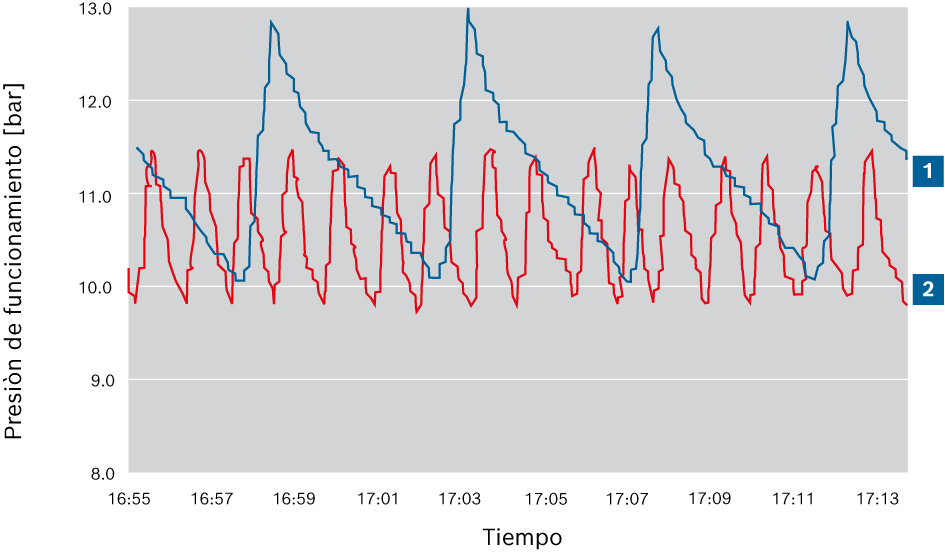
Curva de presión antes y después de ajustar la potencia del quemador
|
Curva de presión antes de regular |
|
Curva de presión después de ajustar |
Preventilación
Antes de cada puesta en marcha del quemador debe garantizarse que no haya mezclas inflamables en los conductos de gases de combustión. Esto se consigue en la práctica mediante la ventilación previa. Antes de que el quemador encienda la llama, el ventilador de aire de combustión se pone en marcha y empuja el aire ambiente a través de los conductos de gases de combustión calientes que todavía están a temperatura de ebullición. Esto calienta el aire frío y extrae calor de la caldera. Se prescribe un cambio de aire suficiente, lo que puede dar lugar a una pérdida de energía no despreciable, especialmente con arranques frecuentes del quemador.
Por regla general, el tiempo de ventilación previa debe dimensionarse de forma que se consiga un cambio de aire de 2 – 3 veces, con referencia a todo el sistema de gases de combustión. El diseño debe acordarse con la autoridad de supervisión técnica. Los arranques frecuentes del quemador no sólo son antieconómicos, sino que también tienen un efecto perjudicial sobre la vida útil. Una situación ideal sería 1 – 2 ciclos de encendido del quemador por hora. Si hay más de 4 ciclos de encendido del quemador por hora, deben tomarse medidas para reducir el número de ciclos de encendido del quemador, por ejemplo, ajustando la potencia del quemador.